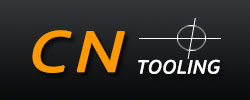 |
|
» What we do? |
» Capacity |
» Quality Control |
|
|
|
News > Die lifetime and die design |
|
Die lifetime and die design | |
Source: www.cntooling.com 5/25/2016 9:25:23 PM | |
|
The lifetime of mold be connected with design level, mold structure,mold's material and treatment, processing and lubricant. According to a large number of statistical analysis for the failed mold, among various failure factors, the irrational structure cause about 25% of die failure,therefore, rational design for the mold structure, it will very helpful to imporve the quality and lifttime of the mold.
No matter what kind of mold, die sets/mould base should have good rigidity, the plate should not be too thin, in the case of a machine enough space to try to increase the thickness, not only to meet the strength requirements of the mold, but also consider in the rigidity of the die sets/mould base.
For multiple-stage die, two guide pillars is often difficult to guarantee the requirements of accuracy, should using four guide pillars, and consider to using six pillars for large dies. While using several guide pillars, should pay high attention the positional accuracy of the relate parts.
For the punch or insert of the mold, the size of forming radius not only affect the forming process and parts quality, but also have an impact on the lifetime of the mold and failure modes. Under the premise of meeting the product requirements to increase working parts forming radius, which increases die lifetime will receive unexpected results. Under the situation that can not increase the radius size or complicated structure, you can consider using mosaic structure, which also can reduce stress concentration.
For stamping die, under the premise that to ensure the dimensional accuracy of parts, increase the gap between convex and concave parts, in order to improve the stress state of the punch, to make punching power, force and stripping force decline, the wearing of punch and insert is reduced, thereby improving the die lifetime.
Pay attention to the problem of waste rebound in high-speed progressive die, optimize the mold structure, in order to avoid the scrap rebound tinily due to a meomentary vacuum while high-speed stamping, it will easy make the insert/punch broken.
For high temperature mold, such as hot forging mold, the cooling problem can not be ignored in the structural design, should avoid the mold's material has plastic deformation due to local temperature is too high.
| |
|
About Caan Precision Tooling, China:
Caan Precision Tooling (DongGuan) Co.,Ltd. was founded in 2007,
which is an enterprise specializes in precision products and
services, supply quality products at competitive prices. We
would like to be your reliable supplier and trusted friends.
Thank you for your attention!
We
have became long-term suppliers for famous enterprises, such as:
TKD, Apple,Green Point, Sony, Chiyoda Integre and so on. You can
refer to:
http://www.cntooling.com
Allen Wang
Caan Precision
Tooling (DongGuan) Co., Ltd.
Address: 87 XinMin
Road, XinMin Community, ChangAn Town, DongGuan City,
GuangDong Province, P.R.C.
E-mail:
info@cntooling.com
Mobile: +86 132 3838 2210
Fax: +86 0769 8908 9111
Website: www.cntooling.com
Skype: allen_cntooling
Facebook: info@cntooling.com
Precision
Tooling |
Chinese Stamping Die Manufacturer|
Chinese mold
|
|
Previous: Precision tooling in china
Next: Causes analysis for mold burst and action
|
|
|
|
|